Engineer’s Corner
Step 1
Check native soil moisture content using field moisture meter in cut soil prior to applying enzyme. Ideal moisture range is between 10-20%
If moisture is above 20%, the soil must be dried utilizing the heat in the drum of the reclaimed through another pass at full depth, or through the use of additives. If moisture is below 10%, water can be applied topically without chemical.
Step 2
After diluting the chemical with water, evenly spray mixture over reclaimed surgace. Due to short working windows, no more than half a mile shoul dbe sprayed at a time. Following application, moisture readings should be taken. Optimum moisture will range between 10-20%
Always fill truck with water before adding chemical. While dilution will be adjusted depending on conditions, 230 gallon water will be used per 1 gallon of chemical.
Step 3
Once optimum moisture and even chemical distribution have been achieved, the surface is ready to be tilled/reclaimed again to full depth.
This allows for the chemical to evenly blend into the base of the road and will start the chemical binding process between the enzyme and aggregate clay soils.
Step 4
In order to complete the chemical process, the road is to be fully packed with pad foot rollers. This will typically take 4 to 5 passes for the chemical to set and bind with the aggregate soils.
It is vital to complete this step immediately following step 3 before the soil dries out. This allows for the chemical to create a proper seal throughout the foundation of the road and will prevent water encroachment for years to come.
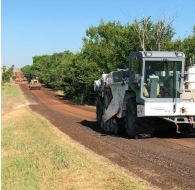
Step 5
Following full compaction, the road is ready to be bladed and shaped to the desired grade. A smooth tire roller/ pneumatic packer can be used to smooth out any rough spots if desired.
The product will set and cure quickly. Depending on heat/humidity, you will have about a 4-hour window to grade the road following the application of the chemical via water truck. It is important to have reclaimer/ackers/blade ready..
Step 6
If aggregate is not the final coat, crushed rock/concrete can be applied immediately. Chi[ and seal or asphalt can be applied 24-48 hours following stabilization. With proper application, the treated road will provide years of service with a fraction of the maintenance costs and time associated with conventional engineered methods.
Road can immediately be opened to light traffic within 4 hours, and heavy traffic after 48 hours.
Calculating SoilPak-250 and Compaction Water Application volumes
Determine compaction water needed to achieve optimum moisture. The target should be no less than plus or minus 2 % of optimum with optimum moisture to be the target. Error on the wet side to assure that you have distributed the chemical throughout the cut. The amount of enzyme to be distributed hold constant with some variations if high moisture rates are encountered. If high, in situ moisture is encountered above optimum moisture level, air drying may be required by turning over soil or making an initial cut with the reclaimer to reduce the soil moisture level prior to chemical distribution. Try to get the moisture level several % points below optimum to assure that ample rate of enzyme can be distributed. (Note: aggregate may have in situ reading of 3-4% while heavy clay soils may have a 20% in situ moisture level.)
Calculate compaction water:
(5280′ X 21′ X .75′(8″)) / 27= 3080 cubic yards of material
Next calculate wt. of soil= 2200 lbs./cubic yard X 3030 cubic yards= 6,666,000 lbs. of soil to be treated
(Wt. will vary with moisture content- aggregate will range between 3000-4000 lbs./cubic yard
Next calculate volume of water required to change wt. by each 1% of water. 3080 cubic yards x 2200 lbs./cubic yard x 1% moisture= 67760 lbs. water
Next convert lbs. water to gallons
Water= 8.34 lbs./gallon fresh water
67760 lbs. water/ 8.34 lbs./ gal.=8124 gallons water required to change 1 %.
Calculate Rate per acre: 110800 sq. ft. / 43560= 2.54 acres
Enzyme rate per acre= 55 gallons/ 2.54 acres= 21.6.8 gallons per acre- hold constant Compaction water per acre= 8124 gallons/ 2.54= 3200 gallons/ acre required for each 1% change
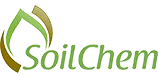
Visit Us
2160 N. Main St. Suite C-35
Newcastle, OK
73065
Contact us
Open Hours
M-F: 9am - 4pm